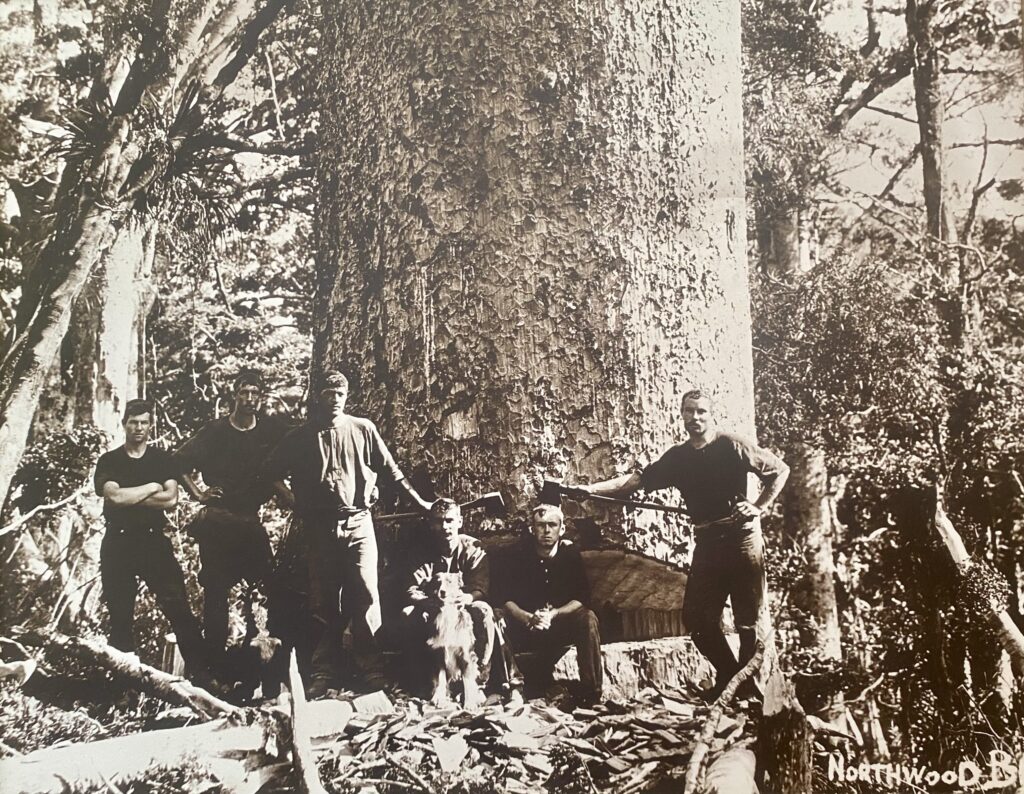
This is another of the Northwood Bros photographic prints that Heather and I managed to save when we closed our craft cooperative Earthworks in 1990. Note the triangular “scarf” cut into the tree behind the men.
§
Transcript of Hugh’s 1950s radio talks, # 2
In my last talk, I discussed the establishment of a bush camp and supplying it—building a shanty, packing in supplies, and so on. In this one, I want to tell you something about the felling of the trees themselves.
When we think of Kauri bushmen, we are inclined to think of a whole lot of men with sharp axes and a couple of long saws, advancing on Kauri trees with the intention of chopping them down. However, it was not quite so simple as that because, in the first place, not all trees in the bush were Kauri; and secondly, the Kauri is a very large tree; and thirdly, it is not always easily accessible.
So, in a bush camp, there were a number of men whose jobs were very different. I have already told you about the pack horsemen and the all-anything important cook. Now, who else was there?
There were the crosscutters. These were the bushmen you think of—they felled the tree, crosscut it into logs, and sniped the ends. Meanwhile, the road makers—the civil engineers of the bush—were preparing bush tracks, skidded roads, and so on, along which the bullock teams, with their teams of, say, 16 bullocks, would haul the logs out to the landings. These landings were on creek banks or wagon roads.
First of all, the crosscutters. They worked in pairs and were equipped with axes, mauls, and wedges. The axes had four- or five-pound heads. Each man had his own axe, on which he lavished great care. An axe, well-ground and with a finely honed edge, was not merely an implement to be proud of but a tool which, in skilled hands, was capable of doing a great job. Likewise, the saw, which would be shared by two crosscutters, called for extra skill in sharpening and maintaining, in a perfect state for good work, so that whereas every man sharpened his own axe, it was usual to have a “saw doctor” in the camp, and it was his business to keep the big crosscut saw in fine trim.
The crosscut saw was from 7 feet to 10 feet in length and was known as a drag tooth saw. This meant that the saw had one hooked tooth and four of the ordinary V-shaped teeth. The drag teeth faced opposite ways, that is, from the centre of the saw, and these hooked teeth were bent towards the handle so that as the sawyer drew the saw towards him, not only did it cut with the tooth, but it also dragged sawdust out of the cut with the drag teeth.
There are many considerations. You probably know that in a simple and uncomplicated operation, you “scarf” the tree on one side—that is, make a deep cut with an axe—then make a short cut from the other side. The tree then falls towards the scarf. But there are not many simple operations of this kind. The ground is not usually level to begin with, and any tree growing on a slope will tend to fall down the slope. It may be necessary to have the tree fall on the upward side in order to get the log out later. Again, it is always necessary to have the tree land on, as far as possible, even ground. A hump, for example, could cause the log to break or split.
All these points and many others must be taken into account by the Bushman when placing his scarf and deciding how deep it must be cut. There are points that apply particularly to the Kauri. Before sawing, the Bushman will ring-bark where the saw cut is to go. This is because the green Kauri tree has a great deal of gum under the bark. This makes a sticky mess on the saw, causing it to jam, so the bark must be removed, along with the gum.
Another question people often ask the old bushman is how he managed to saw through a tree of perhaps 12 feet in diameter with a saw 10 feet long. The answer is, of course, that he didn’t saw through the full 12 feet. The bushman cut two deep scarfs on opposite sides of the tree until he had a thickness which he could operate on. The saw cut would be at right angles to what we might call the “felling scarf”, which, as you remember, is just below the saw cut on the side of the tree that is intended to fall. It is amazing, by the way, how bushmen—not only Kauri bushmen—can fell a tremendous tree within a foot of the place intended, and do it regularly.
Another difficulty, of course, is getting a good standing alongside the tree—that is, a good level foothold for each sawyer, and on the same level. This often meant that a staging had to be built around the tree. In fact, it might be said that more often than not, a stage had to be built upon which the crosscutters could get good standing.
People unfamiliar with Kauris may not realize that one of the special characteristics of the tree is that it has a long trunk, or bole, on which there are no branches at all. In a normal Kauri tree, the branches all come out from the top, in a sort of crown. From a timber point of view, that is, of course, very important. Nowadays, some use is made of portions of the crown, and in fact, some of the larger limbs are cut for timber. But in the early days, nothing was taken above the first limb.
The tree was cut into short lengths, according to two main considerations. The actual diameter of the log—you will remember it had to be hauled by a bullock team—must therefore not be too heavy for the team to pull. The other consideration was where the logs had to go, and what the terrain was like. The rougher the country and the softer the ground, the shorter the logs that must be cut from the tree.
After the logs were cut, each was “sniped”. To snipe the end was to chip all the way around so that it could be hauled without catching on humps in the ground, stumps, and so on. In fact, you might say that a log when it is sniped looks rather like the blunt end of a whale. Very heavy logs were not only sniped but barked as well, so that they would slide more easily from the point where the tree was felled out to the skid tracks, which I will describe later. The bullocks hauled one log at a time, but on the skid road, a maximum load was taken every trip, the number of logs depending on the size.
The gradient of the skid road varied, and when the gradient was easier, as you’ll find when I tell you about the work of the bullock teams, as many as four or even five good-sized logs could be hauled. But in the early days, that would not have happened because nothing under a 6-foot girth was saleable then. Anything smaller than a 6-foot girth was just a “rika” to those boys.
The roads bringing the logs out of the bush from the stump were called the “breaking out roads,” and they were really only bush tracks along which the bullocks hauled the logs out to the main road. The crosscutters’ job was always looked upon as a good job, although it was hard work. It was one of the cleanest, quite interesting, and quite self-contained. Like most bushmen’s jobs, it had an element of danger, but to the skilled men, these held no terrors.
One of the dangers was when a tree was falling through the green bush and smashing down other trees. There was the risk of flying broken branches and splintered wood being hurled back. Another danger that gave no warning, but was well-known to the men, was when a tree was being felled that had its branches interlocked in the branches of another. When a tree starts to fall, its movement at first is slow, and it can be understood that a very slight lift at the stump means the actual tree head has moved. This means that small branches, and sometimes quite large ones, are broken off as they disengage up above. And then, falling from say 100 feet, it can be very serious.
The total equipment of a pair of crosscutters was not very much—consisting of two or three axes, a length of saw, a tape measure, and three or four wedges. As these tools did not cost much, it enabled a couple of men to take such a job on contract—at so much per 100 super feet.
We talk today of the “vandals” of the Kauri forest. Well, if you can visualise a beautiful stand of green Kauri, with say a million feet of timber in it, and then send two of these men in with the few tools I have mentioned, in a matter of a few months it is just a wilderness of broken tree heads and the trunks of the trees and logs. Well, it would have the appearance that some vandal had been at work.
You may have heard the term “tail rope e” in connection with crosscutting. That is when a large tree has been felled and cut, and an extra-long saw is being used. This means that it is very heavy pulling on the saw, and an extra two men are brought in to assist. A short piece of rope, sometimes made of flax or even the Bushman’s belt, is fastened to the handle of the saw, and the second man just pulls on that.
The cutter invariably supplemented his earnings by collecting gum. He would find the heads of the trees where branches had been broken, in the forks of limbs and such places. The ideal crosscutter was the man who could detect a fault in the set of the teeth of his saw, rectify it right away, and always have it sharp. This, of course, meant not only faster work but easier work.
One of the best I ever knew was Jimmy Cross, living at Paparoa. I always had great respect for him because of an incident when I was a very small boy. I picked up his axe to take it to him—put it on my shoulder manlike, but with the blade turned inwards instead of outwards. When he saw me coming with it like that, he stopped me at once and made me turn the axe over. Then he showed me just what would’ve happened if I had tripped—the blade of the axe would’ve got me just where the chicken got it. However, it made such an impression on me that I can still remember that day quite well. Ever since then, if I see anyone carrying an axe in that position, I think of the fright I got.